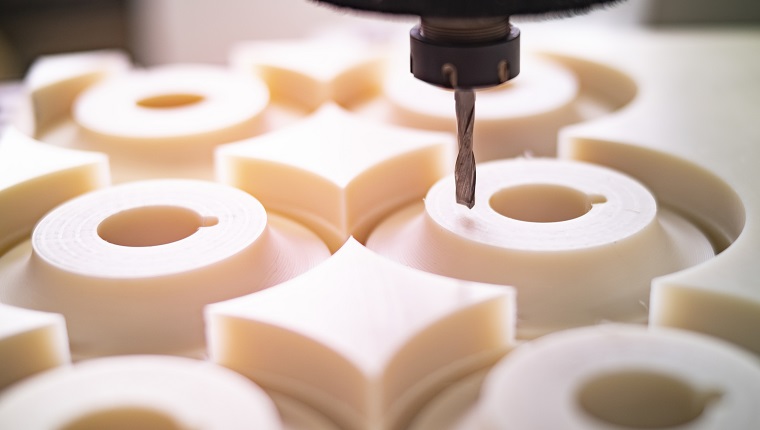
For many manufacturers, challenges arise when setting up production flow for low volume / high variation product lines. Agile Job Shops are those that can accommodate 2000 product variations with production volumes typically below 100 pieces.
Usually, these facilities develop to excel as an Agile Job Shop or they struggle and fail. Fail: with part shortages, long lead times, and/or inventory imbalances.
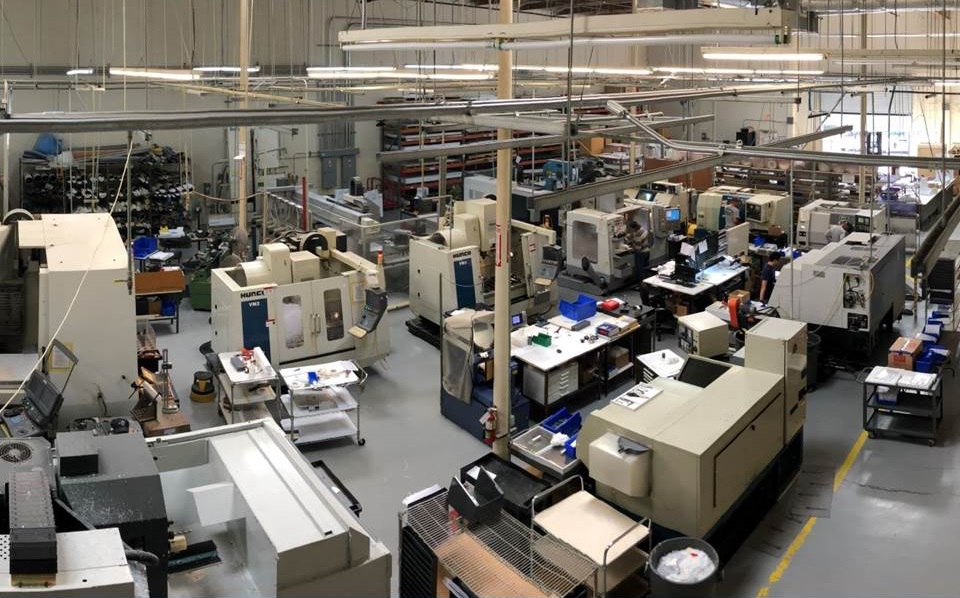
A combination of sound Lean Manufacturing Principles, including a blend of Visual Manufacturing Triggers with Just in Time (JIT) Processes, usually help to ensure the right components are landing in Assembly at the right time.
iPolymer was created from the merger of BECO Manufacturing and TEQCOM Industries. Any given year, iPolymer shipped over 2000 unique SKUs with most production volumes under 100 pieces. Our Manufacturing Processes were designed to ensure the correct blend of components arrived within a week or two from their required date into Assembly.
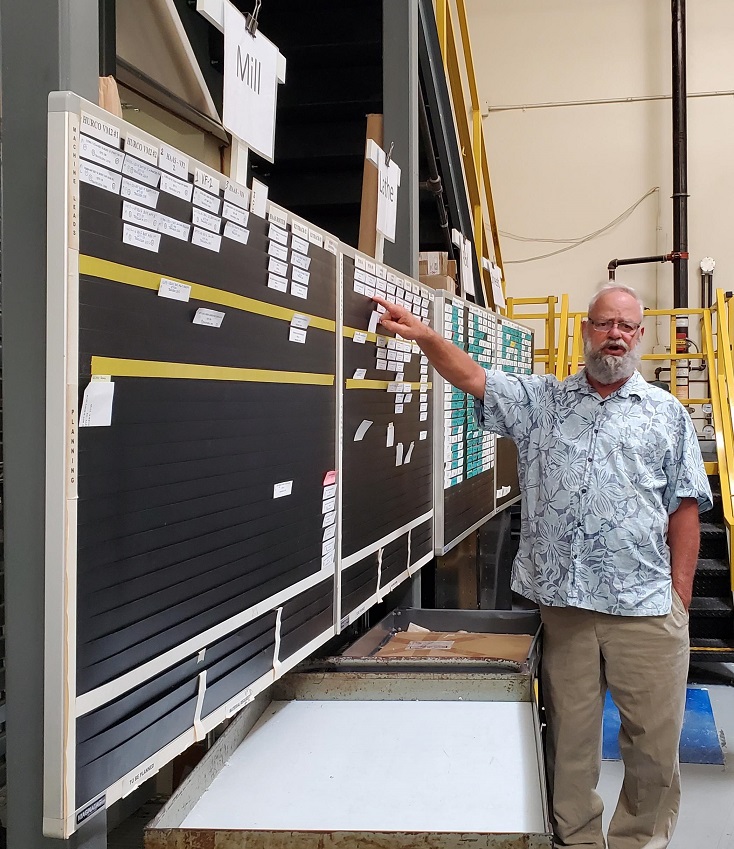
Visual Production Job Board helps enhance middle-tier ERP Systems. The visual characteristic ensures the production team senses the flow of their manufacturing process.
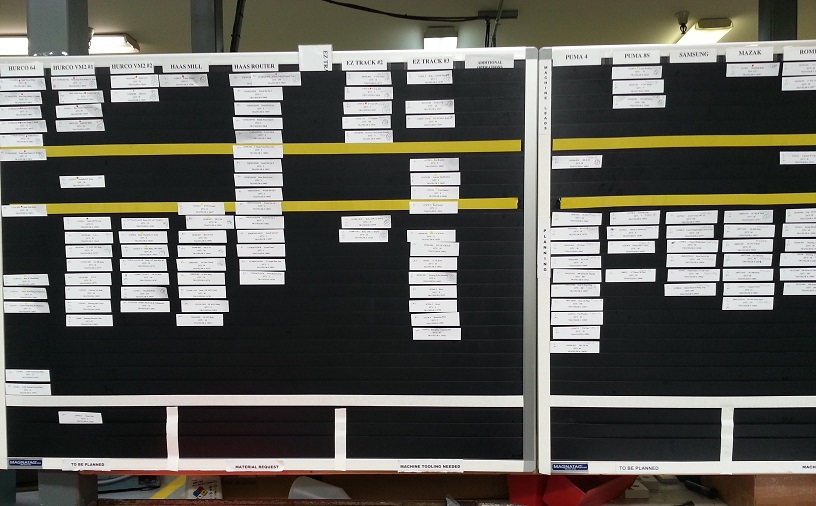
Breaking up the manufacturing process into individual stages with Visual Queues creates a simple roadmap to our production flow. Unique scheduling/status boards are staged at each queuing point.
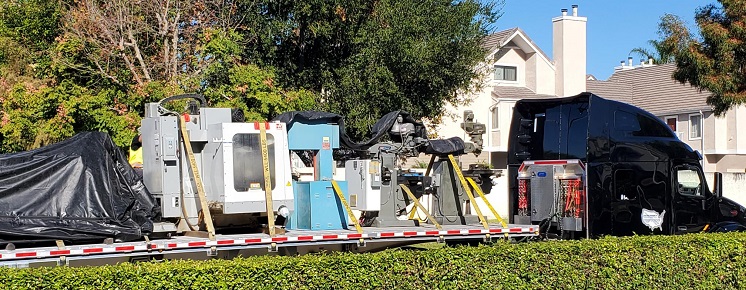
Agile Job Shops, supporting high component variation at low volumes with quick lead times, require an abundance of machine Tools. Machine Tools that can be set up by one machinist in under 100-minutes significantly help the short run production model. Assuming 100-piece nominal production run: a 100-minute setup adds one minute, or less, to the Costed Bill of Material – the run time would also be added to this figure.
